brake forming sheet metal Press brakes are indispensable machines in the metal fabrication industry, enabling precise bending and forming of sheet metal to create a wide range of structures and components. These versatile tools are classified into three main categories: mechanical, hydraulic, and . $30.21
0 · homemade sheet metal bending brake
1 · hobby sheet metal brake
2 · hobby sheet metal bender
3 · harbor freight sheet metal brake
4 · harbor freight 36 inch brake
5 · harbor freight 30 inch brakes
6 · harbor freight 30 inch bending brake
7 · 30 in mountable bending brake
Midea MOR17BSA-SS 1.7 Cu.ft. Over The Range Microwave Oven with Smart Touch Panel, Auto Cooking Menu, 1000 W, 300 CFM Ventilation, in Stainless Steel
Press brakes are indispensable machines in the metal fabrication industry, enabling precise bending and forming of sheet metal to create a wide . Press brake bending involves leveraging force to shape sheet metal into desired geometries. Two vital concepts in press brake bending are K-factor and the neutral axis. Understanding these elements is crucial for achieving precise and repeatable bending operations. Press brakes are indispensable machines in the metal fabrication industry, enabling precise bending and forming of sheet metal to create a wide range of structures and components. These versatile tools are classified into three main categories: mechanical, hydraulic, and .Get an Eastwood DIY sheet metal brake to bend and shape sheet metal accurately for custom car parts accessories. We carry DIY sheet metal brakes in all forms.
Press Brake Forming Process. The forming with the press brake exemplifies precision and flexibility. In manufacturing, it is a must-have method for shaping sheet metal. Here’s how the forming process takes place: Preparation; The first step is to get a flat metal sheet ready. Stainless steel, aluminum, or steel are common materials for the .Powered by an advanced CNC control system, the AutoBrake ® sheet metal brake by Roper Whitney is capable of bending many types of materials and thicknesses with very little setup time and minimal tool changes.
The Eastwood Manual Sheet Metal Brake is the simplest, most efficient way to form bends and creases in panels. In addition to standard variable-length bends, it also can do ½-inch offset bends up to 90 degrees.GMC Machine Tools sells sheet metal bending brakes, perfect for any fabrication shop looking to bend sheet metal. Create simple bends and creases by slidding the workpiece between the clamping bar and bending leaf.Provided in varying bending lengths, WWF’s straight sheet metal brakes assure effortless and smooth bending for sheet metal of varying thicknesses such as 18, 20, and 22 gauge capacity mild steel, 16 gauge (1/16") aluminum, and more.Shape sheet metal using your bench vise as a sturdy base. Remove or slide the four dies along the clamping bar to form angles, channels, boxes, trays, and pans in a variety of widths. Unlike bench-top and floor-mount benders, these are not permanently mounted— pull them out when you need them and store them when you don’t. Max. Bending Wd. For Max.
In the 1920s, forming changed from folding on a leaf brake to forming into a V die with a matching punch. A 90-degree punch would be coupled with a 90-degree V die. The change from folding to forming was a major leap forward for sheet metal.
homemade sheet metal bending brake
Press brake bending involves leveraging force to shape sheet metal into desired geometries. Two vital concepts in press brake bending are K-factor and the neutral axis. Understanding these elements is crucial for achieving precise and repeatable bending operations. Press brakes are indispensable machines in the metal fabrication industry, enabling precise bending and forming of sheet metal to create a wide range of structures and components. These versatile tools are classified into three main categories: mechanical, hydraulic, and .Get an Eastwood DIY sheet metal brake to bend and shape sheet metal accurately for custom car parts accessories. We carry DIY sheet metal brakes in all forms.Press Brake Forming Process. The forming with the press brake exemplifies precision and flexibility. In manufacturing, it is a must-have method for shaping sheet metal. Here’s how the forming process takes place: Preparation; The first step is to get a flat metal sheet ready. Stainless steel, aluminum, or steel are common materials for the .
Powered by an advanced CNC control system, the AutoBrake ® sheet metal brake by Roper Whitney is capable of bending many types of materials and thicknesses with very little setup time and minimal tool changes.
The Eastwood Manual Sheet Metal Brake is the simplest, most efficient way to form bends and creases in panels. In addition to standard variable-length bends, it also can do ½-inch offset bends up to 90 degrees.
GMC Machine Tools sells sheet metal bending brakes, perfect for any fabrication shop looking to bend sheet metal. Create simple bends and creases by slidding the workpiece between the clamping bar and bending leaf.
hobby sheet metal brake
hobby sheet metal bender
harbor freight sheet metal brake
Provided in varying bending lengths, WWF’s straight sheet metal brakes assure effortless and smooth bending for sheet metal of varying thicknesses such as 18, 20, and 22 gauge capacity mild steel, 16 gauge (1/16") aluminum, and more.Shape sheet metal using your bench vise as a sturdy base. Remove or slide the four dies along the clamping bar to form angles, channels, boxes, trays, and pans in a variety of widths. Unlike bench-top and floor-mount benders, these are not permanently mounted— pull them out when you need them and store them when you don’t. Max. Bending Wd. For Max.
pvc-u flame retardant electrical enclosure oem
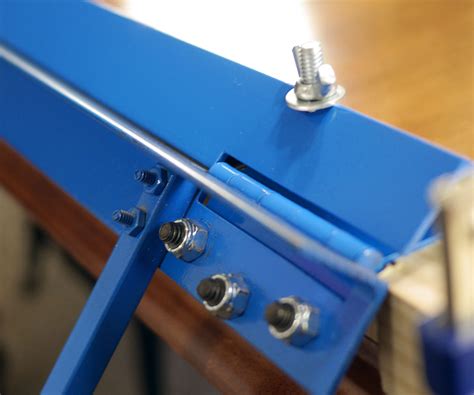
qualified metal fabricators kernersville
IP68 Waterproof Junction Box Outdoor, 3 Way Underground Electrical Junction Box, Plastic Electrical Box with Terminal Block, Suitable for LED Landscape Lighting, Garden Lights, Solar Power and More
brake forming sheet metal|30 in mountable bending brake